Your gas panel design guide: Key considerations for industrial applications
Learn about the importance of gas panel design to ensure safety, efficiency and reliability.
Gas distribution systems are widely used in industrial facilities in the Netherlands within industries such as petrochemicals, semiconductors and biotechnology. Gas distribution systems typically consist of four subsystems:
- Source inlet connection
- Primary gas pressure control (gas control panel)
- Point of use
- Automatic changeover
The system as a whole must deliver gases safely and effectively from a high-pressure source to the point of use at a specific pressure and flow rate. Gas control panels are the first stage of managing high-pressure gases and act as the primary pressure control point and therefore need special attention.
Below, our gas panel design guide describes the basics of gas control panels and key considerations when looking for a replacement or new panel for a gas distribution system.
Gas panel design guide: the basics
Gas panels-the primary pressure control point in gas diffusion systems-are located near the gas source (gas cylinder). Gas control panels reduce the pressure of the cylinder to deliver the gas to the next stage of the gas diffusion network at the appropriate pressure and flow rate, where it is then delivered to the point of use.
The point of use can range from analyzers to process equipment to laboratories, depending on the specific application. Below is an example of how gas panels can be incorporated into a gas diffusion system for an analytical instrumentation shelter.
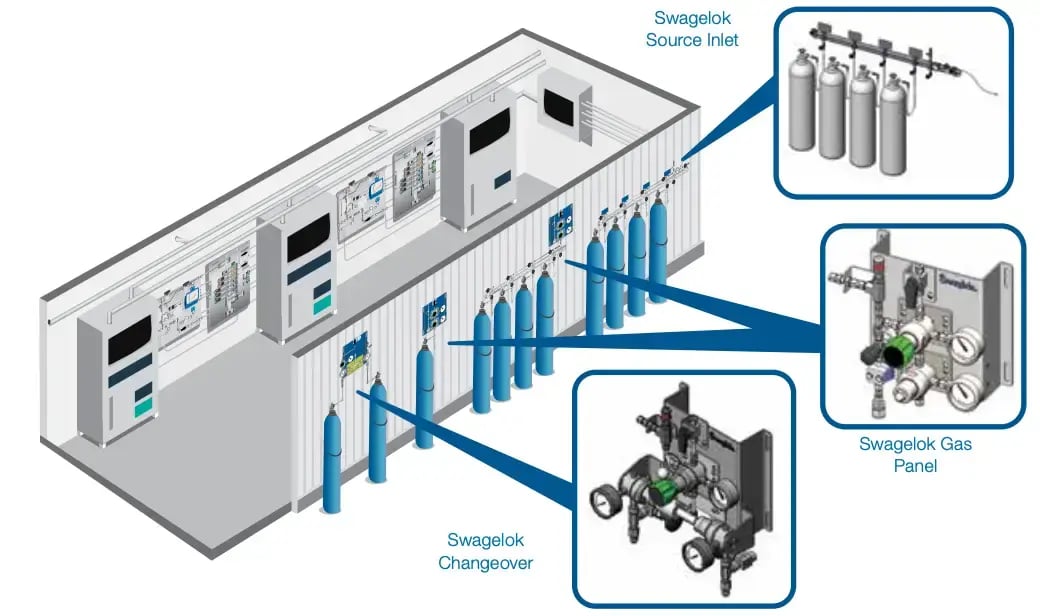
Gas panels reduce cylinder pressure through a single- or double-stage pressure regulator. Careful selection and sizing of pressure regulators are critical to maintaining a functioning gas distribution system.
Gas panel design guide: key considerations
When installing a new gas control panel for a gas distribution system, there are several important considerations that can help ensure:
- The gas is properly reduced to the specified pressure and flow rate
- The panel is easy to install, operate and maintain
- Employee and environmental safety is ensured
- Reliability is maximized to minimize downtime
Considerations for pressure regulators
The most important factor for an effective gas control panel is the proper selection of a pressure regulator. To understand how to make this selection, it is important to understand these four aspects of pressure regulator performance:
- Droop: The "flat" middle portion of the flow curve below is actually nonlinear and slopes downward - this is known as droop. Depending on the pressure regulator selected, the outlet pressure will drop to some extent as the flow demand increases.
- Seat-load drop and lock-up: the small first portion of the curve (shown: from left to right) shows seat-load drop and is the initial pressure drop that occurs when a regulator starts from a zero flow condition. Looking at the same portion of the curve from right to left, this is known as lock-up, characterized by an increase in outlet pressure when flow is reduced to zero.
- Choked flow: the steep negative slope on the right side of the curve below shows choked flow. This occurs when the flow demand is greater than the pressure control capacities of the pressure regulator.
- Supply-pressure effect: this effect is characterized by the change in regulator pressure as a function of the change in inlet pressure.
Below is a typical flow curve for a pressure reducing regulator that demonstrates the above aspects.
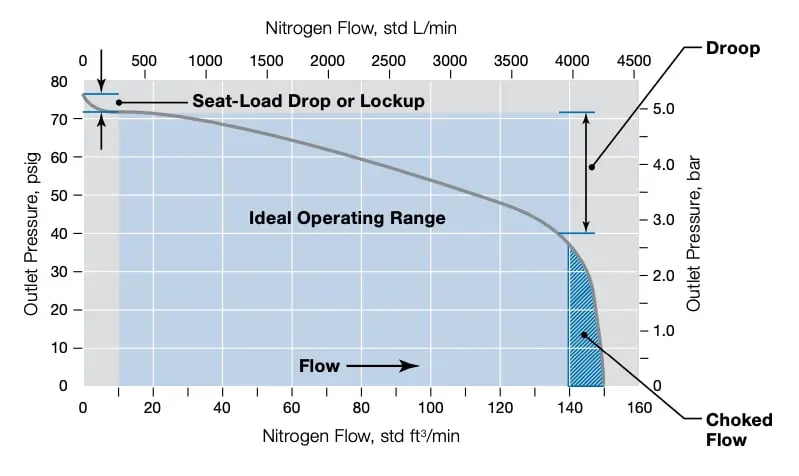
Single-stage pressure regulators reduce cylinder gas pressure within a given range in one step, while double-stage completes this process in two steps.
The above aspects of pressure regulator performance vary between single-stage and double-stage pressure regulators. For example, single-stage pressure regulators typically exhibit minimal droop at varying flow rates, but may exhibit a high supply-pressure effect. On the other hand, double-stage pressure regulators typically exhibit minimal supply-pressure effects, but may exhibit a steeper slope in droop. To correctly determine the correct regulator and sizing, it is necessary to calculate the correct gas pressure and flow rates.

Single-stage

Double-stage
Proper calculation of gas pressure and flow Rate
A wide range of gases are used in gas dispersion systems within the petrochemical, semiconductor and biotechnology industries. Common gases include hydrogen, nitrogen, carbon dioxide, oxygen, helium, argon and propane, and exotic gases such as bromine, titanium tetrachloride and phosphorus trifluoride. The calculation of flow and pressure depends on the type of gas and various process aspects. This calculation is critical to the proper operation of pressure regulators and gas panels. An expert in fluid systems should be consulted to help with this calculation and ensure that the correct pressure regulator is selected.
Gas panel layout
Using a custom gas control panel design specific to applications can reduce the potential for leaks and provide ease of operation and maintenance. Leaks often result from an excessive number of connections. Since each connection must be treated as a potential leak point, special fittings and connectors can be used to eliminate additional connections, minimizing the number of potential leak points in the design. Leaks often mean wasted money for industrial facilities, in addition to posing a safety risk when toxic gases are dispersed.
An intuitive and clearly labeled panel can promote correct operation and minimize the risk of operating errors. Panels that are modularly designed are easy to maintain when maintenance is required, minimizing downtime.
Components and instrumentation
The implementation of a standardized, but configurable, backplate allows the panel to work with standard cylinder sizes and meet configuration requirements as determined by specific applications. Gas control panels shall include and be capable of including upstream and downstream pressure indicators:
- Pressure relief valves
- Ball valves
- Non-rotating needle valves
- Piping and fittings
Construction materials may vary depending on the application, type of gas and operating conditions.
Safety of operator and environment
When supplying gases that can be harmful to operators and the environment in the event of a leak, it is important to mitigate safety risks to ensure operator safety and avoid potential penalties. Although catastrophic leaks are rare, restricted flow vents can be placed near the gas source, limiting the maximum flow and providing an additional level of protection.
Temperature and pressure ratings for components within a gas panel must match process requirements to ensure safe operations. In addition, components such as valves may have the same rating, but one may be better suited for a specific application. Pressure regulators and relief valves must be sized to accommodate the full range of potential flow rates and pressures.
Reliability
Since gas distribution systems play an important role in industrial facilities and gas control panels are the primary pressure control system, the reliability of gas panels is critical. Unreliable gas panels can affect equipment, processes or laboratories that depend on the gas diffusion system to deliver a particular gas. This can result in equipment damage or maintenance, leading to downtime of various processes in industrial facilities. Throughout the life cycle of gas dispersion systems, reliable gas panels must prevent leaks and wear on components and deliver gas within the appropriate amperage and pressure ranges required for a given application.
Supporting future changes in process conditions
Process conditions for many industrial applications are likely to change over time. Therefore, designing to accommodate such future changes can prevent the need to replace or modify pressure control components in the future. Pressure control components, including pressure relief valves and pressure regulators, can be sized to support a wider range of flow rates and pressures, providing flexibility to meet future process conditions. However, sizing pressure control components to support too wide a range may result in poor performance within the main range. Therefore, careful consideration is required to correctly size pressure control components to maintain high performance within the main range of pressures and flow strengths while accommodating conditions outside that range.
Your local designer and manufacturer of gas panels: Swagelok Netherlands
We design, manufacture and test gas distribution systems for customers, here in Waddinxveen
Read more
Read the additional pages below about Gas distribution systems