How corrosives imperceptibly affect the efficiency of your plant
Having efficiently operating plants with as few downtime moments as possible is highly desirable within the gas/oil and petro/chemical industries. Corrosion is a common problem in this regard. It is a natural process that occurs when certain materials, especially metals, react with their environment, leading to gradual deterioration. Learn in this blog what corrosion is, where it often occurs in a plant and how it can be prevented.
What is corrosion ?
The most well-known type of corrosion is iron rusting, which happens when iron reacts with oxygen and moisture in the air. This results in the formation of iron oxide, a flaky and reddish-brown substance that over time weakens the metal's structure. Similarly, other metals can also corrode when exposed to their respective corrosive elements.
Corrosion can have significant adverse effects on various industries, structures and equipment, leading to reduced structural integrity, decreased performance and potential safety hazards. Preventive measures such as the use of corrosion-resistant materials, coatings and regular maintenance can help reduce the impact of corrosion and extend the life of metal components.
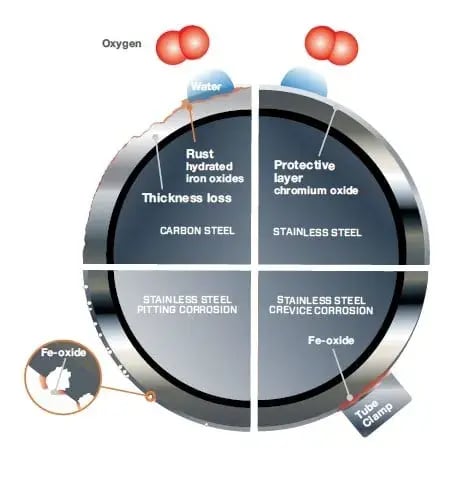
How do you prevent corrosion in your facility?
Rusting, corrosion is an extremely costly problem. Damage from uncontrolled corrosion to pipe systems or instrumentation is a major cause of lost profits in industrial applications, often offshore. Costs for this add up to billions per year. Rusting can be prevented as long as companies know what to look for and take preventive measures to reduce the risks of corrosion before it is too late. Almost every metal used in our world corrodes under certain conditions.
There are steps that can be taken to prevent corrosion in oil and gas applications.
- Identify the different types of corrosion - what it looks like, where it occurs and why it happens
- Select materials that are resistant to corrosion
- Minimize locations where corrosion can occur and limit contact with incompatible metals
The most effective way to prevent a problem is to detect it before it occurs. This can be accomplished by implementing rigorous quality control measures for corrosion prevention, starting with process controls and inspection of the material being used. Inspection can take many forms, ranging from visual inspection to identify surface defects, to the use of non-destructive testing techniques and specialized tests to detect susceptibility to corrosion. It is essential to perform these inspections on a regular basis to ensure that your plant remains free of corrosion and continues to function optimally.
View this TechTalk on "engineered combinations"
Spoken language is Dutch.
Corrosion resistance as a minimum requirement
Another way to verify material suitability is to check for levels of specific elements in the material's composition. For corrosion resistance, strength, weldability and ductility, the starting point is an optimized alloy composition.
As an example, greater amounts of nickel (Ni) and chromium (Cr) in Type 316 stainless steel than are minimally required by the standard specifications of the American Society of Testing and Materials (now ASTM International), result in materials with better corrosion resistance.
A supplier must always provide the chemical composition of a material and indicate that it meets the standards published by the International Standards Organization (ISO) and ASTM International.