The benefits of on-site technical experts
How technical support can help semiconductor manufacturing: a Q&A with Global Field Engineering Manager Greg Mlynar
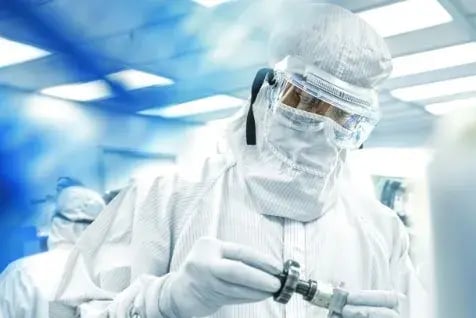
With the need for shorter supply chains and sourcing of materials, availability and the rapid pace of new plant construction, chip manufacturers need solutions to be accurate. And as standardization of processes and facilities becomes more important and demand for semiconductor chips continues to grow, so does the need for engineering expertise and materials localization. It is one reason why third-party technical assistance can be invaluable as an integrated aspect of well-functioning operational teams. In particular, critical gas and liquid systems with a need for high cleanliness can have a major impact on the plant's ability to produce as efficiently as possible. Internal expertise on how to optimize such systems is not always available. Greg Mlynar (GM) of Swagelok, who leads a semiconductor field engineering team, says semiconductor manufacturers can use external expertise when building new plants or revamping existing ones.
LEARN MORE ABOUT FIELD ENGINEERING SERVICES
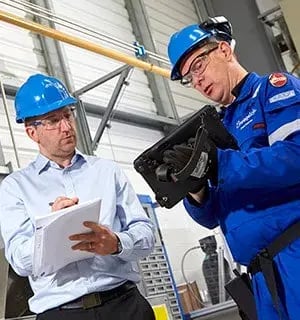
What are the main areas where semiconductor manufacturers can typically use engineering help?
GM: Most semiconductor manufacturers want to improve their processes in every way possible to improve productivity, reliability and efficiency. And that's where outside specialists can provide expertise, especially with gas and liquid delivery systems and applications. Three key areas are of particular importance:
- specifying the right high-purity components for critical equipment
- making improvements to existing gas and fluid systems that will maximize performance
- maintaining gas and fluid systems on-site to ensure consistent throughput.
Because no two semiconductor manufacturing strategies are exactly alike, having a third-party , can evaluate your company's specific needs and recommend a customized solution. This is based on your desired results leading to significant improvements.
Can you explain some of these customized solutions? How are they developed?
GM: Most fabs are looking for support around existing systems to make necessary modifications or optimizations. For example,our team of on-site engineers will assess specific systems, along with all associated hoses, fittings and connections, and then map those systems. They identify opportunities to change or improve them. Through reporting, insights are offered to customers targeted for customized solutions and assembly recommendations.
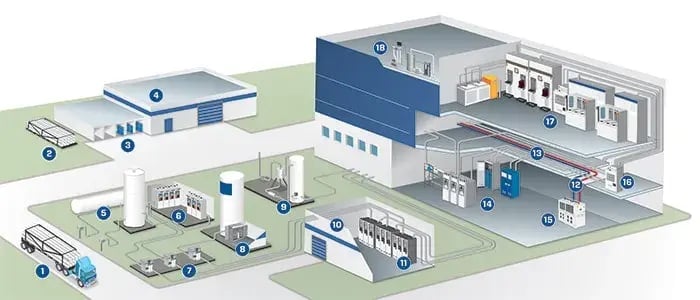
1 Bulk gas transportation 2 Bulkgas cylinders 3 Gas bottle storage shed 4 Bulk gas storage shed 5 Bulk gas storage 6 Bulk gas conditioning |
7 Gas conditioning equipment 8 Gas conditioning equipment 9 Bulk gas silo 10 Bulk Gas Containment Room 11 Gas cabinets 12 Insulated cooling hoses |
13 Hoses for gas supply 14 Special gas cabinets 15 Chiller/heat exchanger 16 Valve Island Boxes 17 Process aids 18 Takeaway |
Depending on your supplier's capabilities, further support may also be available for project design and specification. Ensuring compliance with existing codes and regulations and analyzing the operation of. Providing maintenance for chemical, process gas, water and waste collection systems and performing failure mode and effect analysis (FMEA) on facility systems. As well as support system startup, optimization and shutdown.
Why is this type of support so important?
GM: Because demand in the industry is so high right now, system failures, malfunctions or other emergencies can put semiconductor plants at financial risk. An outside technical team can provide direction to restore operations quickly and safely, implement training for operations personnel and other personnel, and more. But getting new facilities online is also important. For example, our team is increasingly focused on helping our customers with new construction. We are involved in building the base, installing equipment and tools, as well as any necessary start-up installations required for a particular design.
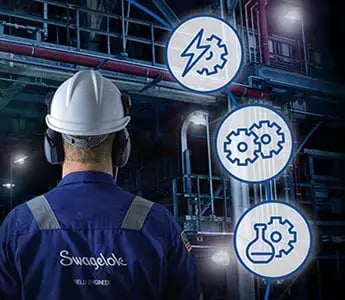
What types of skills should you look for when evaluating an outside technical team?
GM: Technical backgrounds are useful because of the precise nature of semiconductor manufacturing. Electrical, mechanical and chemical engineering disciplines are very applicable to the industry. These are some of the skills that Swagelok's on-site engineers can offer our semiconductor customers around the world.
A deep understanding of how and why certain products and solutions can be ideal for semiconductor applications is also important. These are very demanding systems that handle harsh chemicals. Off-the-shelf components that work in general industrial applications will not always be ideal here. A thorough knowledge of materials science, corrosion types and corrosion-resistant alloys are very helpful in solving challenges inherent in semiconductor manufacturing.
"Working with specialized engineering teams for gas and liquid systems can be a huge time saver.And when time is money, that makes a big difference."
What are some of the biggest benefits that can be realized by working with a specialized engineering team for gas and liquid systems?
GM: First of all, it's a huge time saver. And if time is money, that makes a big difference. Also, with a lot of emphasis on getting new fabs up and running, products and services are accelerated because a failing gas and fluid system could stop the entire $5 billion to $10 billion plant installation. That means nothing is running, no work is being done and no money is being made. That's where specialized engineers can provide the greatest benefit to the customer. Installing the right products to get systems working, then assessing those systems and making recommendations for future enhancements and modifications.
.webp?width=700&height=275&name=blog061_photography-field-engine%20(1).webp)
Semiconductor factories can benefit significantly from the specific insights and technical knowledge that specialized teams can provide.
Want to know more? Swagelok's engineering team has extensive experience integrating with semiconductor manufacturers when building new plants or optimizing existing ones, enabling them to overcome the challenges of gas and liquid systems when pursuing optimized production.
Greg Mlynar has an engineering background, with a bachelor's degree in chemical engineering, a master's degree in microelectronics engineering and an MBA. He has worked in the semiconductor industry for 25 years and joined Swagelok in 2020 as global semiconductor field engineering manager. In this role, Greg leads Swagelok's international team of semiconductor engineers working with fabs, OEMs and material suppliers around the world. He coaches and mentors on-site engineers in the areas of technical services and sales.
You May Also Like
These Related Stories
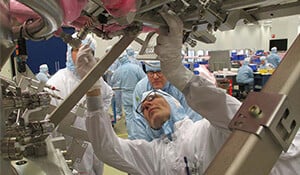
External support lowers costs in semiconductor industry

How to Detect and Prevent Fluid System Leaks
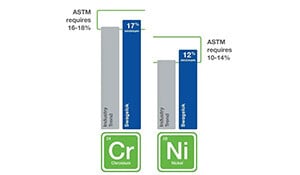